The Material Request Module
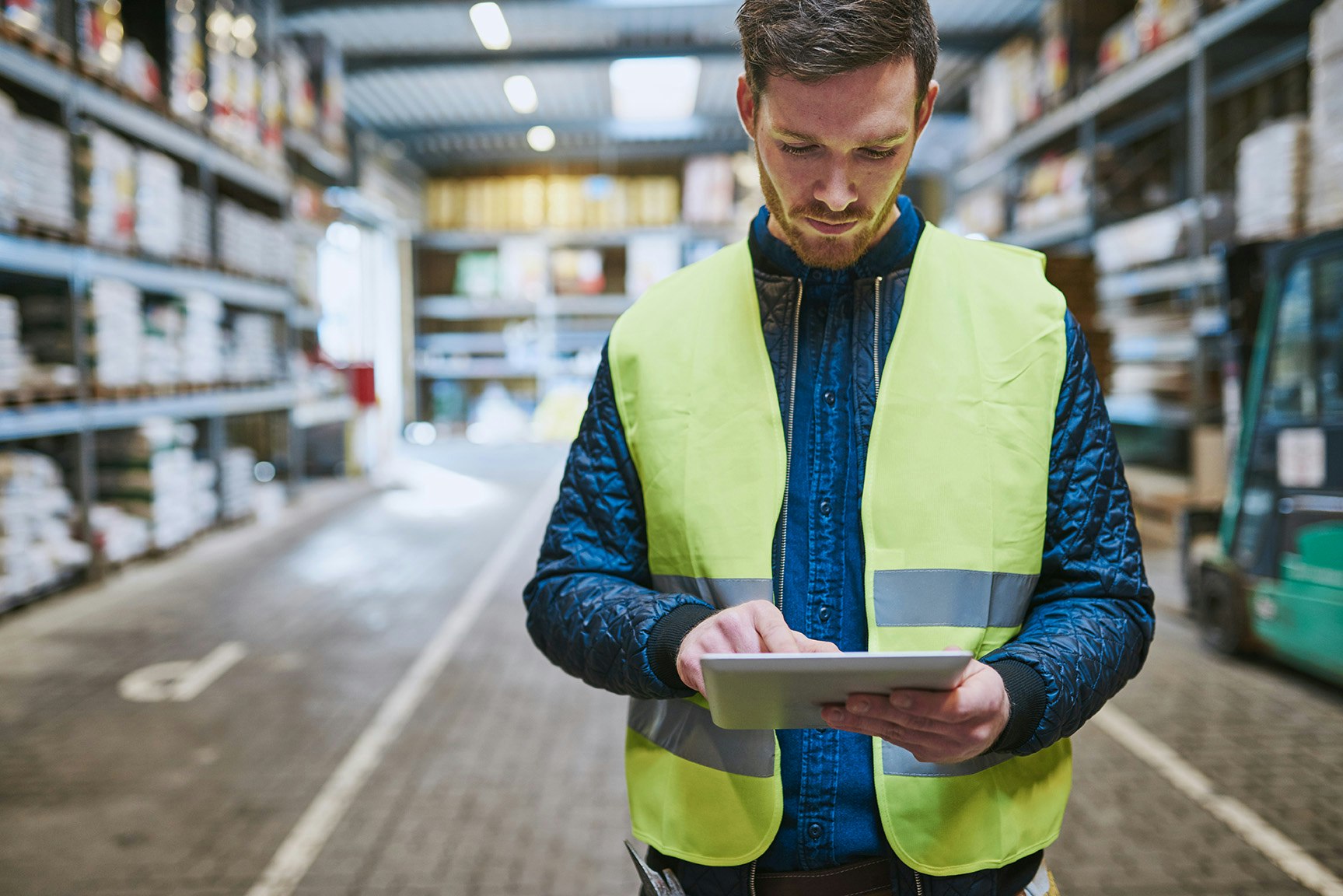
Features and Functions
Since Bill of Material does not indicate Site or Location at the line-item level, PM Tasking and Job Plan modeling functions generate the MR from the current User’s Session Default Company and Location values. It is imperative that the Default Company and Location be defined on the User record for anyone performing PM Tasking or Job Plan modeling.
Like an Inventory Adjustment Issue, a MR must be charged to a GL Account and optionally, a WO Step and/or Project Task. If a WO Step or Project Task is entered, its associated GL Account will also be loaded into the MR by default.