In today’s competitive and technologically advanced industries, ensuring the reliability of assets while controlling costs is crucial. A Computerized Maintenance Management System (CMMS) plays a pivotal role in achieving these goals by streamlining maintenance processes, reducing equipment downtime, and improving safety standards. When properly deployed, CMMS applications become an essential part of asset management strategies, optimizing both cost-efficiency and safety performance.
How CMMS Applications Reduce Maintenance Costs
1. Preventive Maintenance Planning
One of the primary functions of a CMMS is to facilitate preventive maintenance (PM). Rather than reacting to equipment failures after they occur, CMMS allows maintenance teams to schedule regular inspections and service tasks based on the manufacturer’s recommendations or asset performance data. This approach minimizes unscheduled downtime, reduces the frequency of costly repairs and extends the lifecycle of machinery.
Example: A properly deployed CMMS will trigger alerts when a piece of equipment is due for service, ensuring that parts are replaced before they wear out or cause larger system failures.
2. Optimized Resource Allocation
CMMS applications help organizations allocate resources such as labor, spare parts, and tools more efficiently. The system tracks technician availability, skill sets and task requirements to assign the right personnel to the right jobs. This reduces overstaffing, minimizes wasted time and optimizes work completion rates.
Example: The system can automate work orders, ensuring that the most critical tasks are prioritized, while also tracking the exact number of labor hours and materials used, providing insights for cost savings.
3. Inventory and Spare Parts Management
A CMMS helps manage spare parts inventory by tracking usage rates and automatically reordering parts when stock is low. This eliminates unnecessary purchases and reduces the risk of stockouts, which can delay repairs and lead to prolonged downtime.
Example: By analyzing historical data on part usage, the CMMS ensures that the maintenance team orders the correct quantities of spare parts, reducing the financial burden of holding excess inventory.
4. Reduced Equipment Downtime
Minimizing equipment downtime directly correlates with reduced maintenance costs. CMMS applications monitor asset performance in real-time, identifying trends that might indicate impending failures. This predictive capability enables maintenance teams to take corrective action before major breakdowns occur, thus reducing the cost associated with emergency repairs or asset replacement.
How CMMS Applications Increase Safety
1. Compliance with Safety Regulations
CMMS helps ensure compliance with regulatory safety standards by automatically scheduling inspections and audits, generating compliance reports and ensuring timely documentation of maintenance activities. This reduces the risk of non-compliance, fines and accidents related to unsafe equipment.
Example: A CMMS can be configured to notify the team when safety checks for critical equipment are due, helping the organization maintain up-to-date safety certifications.
2. Improved Risk Management
By regularly maintaining equipment and keeping it in optimal condition, CMMS reduces the likelihood of failures that can lead to accidents, injuries, or hazardous conditions. The software allows organizations to track and mitigate risks associated with aging assets, environmental factors and operating conditions.
Example: Equipment with known safety risks, such as high-pressure systems, can be regularly inspected and tested through preventive maintenance plans managed by the CMMS.
3. Accurate Reporting and Incident Tracking
CMMS applications provide detailed reporting capabilities that allow organizations to track incidents and near-misses related to equipment failures. This data can be analyzed to identify patterns and causes, enabling proactive safety improvements.
Example: Maintenance logs in the CMMS may highlight recurring failures in a specific piece of machinery, prompting an investigation that uncovers a safety flaw, leading to corrective action and improved safety protocols.
4. Employee Training and Certification Management
A CMMS can track the training and certification status of employees, ensuring that only qualified personnel are assigned to tasks involving high-risk equipment. This helps to prevent accidents resulting from improper handling or operation.
Example: The system alerts management when a technician’s certification is about to expire, ensuring that no unqualified personnel are deployed for hazardous tasks.
Best Practices for Proper CMMS Deployment
- Thorough Planning: Successful CMMS deployment starts with clearly defined goals. Understand what assets need to be managed, which maintenance processes need improvement and how the system will integrate with existing workflows.
- Data Integration: Ensure that all relevant data from existing systems (manual logs, spreadsheets, or legacy software) is transferred into the new CMMS platform. This ensures continuity and accuracy in tracking maintenance activities and asset performance.
- User Training: CMMS is only as effective as the people using it. Provide comprehensive training to all users, from technicians to management, to ensure they understand how to fully utilize the system’s capabilities.
- Customization: Tailor the CMMS to your organization’s specific needs. Every industry, and even individual organizations, has unique maintenance challenges. Configure the software to address these challenges directly.
- Continuous Monitoring and Updates: Like any software solution, CMMS requires regular updates to improve functionality and adapt to changing maintenance needs. Regularly monitor the system’s performance and update it to ensure it remains efficient and relevant.
Properly deployed CMMS applications can significantly reduce maintenance costs and improve workplace safety. By automating preventive maintenance, optimizing resource allocation, managing inventory, and ensuring compliance with safety regulations, CMMS provides a strategic advantage to organizations. A well-implemented system not only extends the lifespan of assets and reduces downtime but also creates a safer work environment for employees, making it a win-win solution for any maintenance-intensive industry.
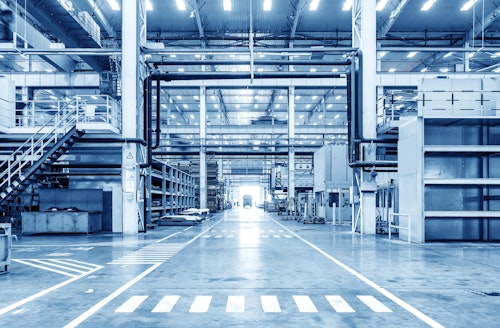
CHAMPS Software