Maintenance teams are well known fixers, rebuilders, and restorers. However, when maintenance is not given proper care and attention, things can quickly turn awry.
And we’re not just talking production mishaps. There are far worse outcomes. EU OSHA states that around 10-15% of all fatal accidents are related to maintenance errors.
Let’s take a closer look at some of these maintenance mishaps, the role that maintenance played in causing them, and how to avoid them.
Not following LOTO
The term “lockout tagout” refers specifically to procedures used to ensure that equipment is shut down and inoperable until maintenance or repair work is completed. They are used to keep employees safe from equipment or machinery that could injure or kill them if not managed correctly. CHAMPS lockout tagout module is designed to make your procedures easy to build, manage, and access so you don’t have to worry about losing paperwork or sharing folders across the company! Plus having images built in to the procedures limits the chances that something will be missed.
Lack of proper training
Many incidents arise from workers not following proper procedures. In some cases, the workers are trying to cut corners. In others, they are pressured to speed up their maintenance activities.
When certain steps are critical, there must be additional safeguards in place. These could be as basic as establishing maintenance approval forms, where every job has a checklist that must be verified by another person of authority.
A common practice of breaking procedures
When workers deviate from established written policies the results can be disastrous. The correction is not simply to tell employees to follow procedures, instead you have to find the root cause and address it.
Cutting corners due to time constraints
The cause for this incident is once again rooted in not following procedures. When the maintenance crews found abnormalities, they paused and tried to understand the situation. But their management pushed them to finish the job. Instead, they should have followed proper safety measures to determine the discrepancy and the arc source.
Maintenance execution lacking expertise and rigor
Many businesses make attempts to build a safety program, but ultimately fail because they do not follow through properly. This could be due to a lack of experience, resourcing, or knowledge.
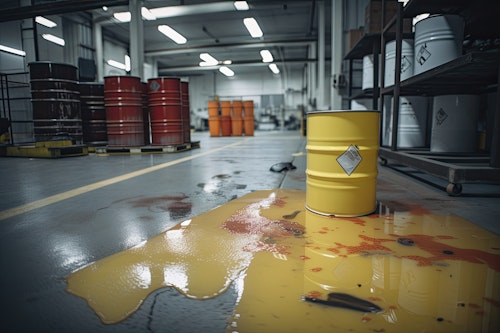
CHAMPS Software